Master Production Scheduling and Dependent Demand Planning: A Comprehensive Approach to Efficient Operations
Effective supply chain and operations planning rely on three critical processes: Master Production Scheduling (MPS), Material Requirements Planning (MRP), and Rough Cut Capacity Planning (RCCP). Together, these processes help companies plan production, manage raw materials, and optimize capacity to align with customer demand and ensure efficient use of resources. Let’s explore each process and how they work together to streamline operations.
Master Production Scheduling (MPS)
Master Production Scheduling (MPS) serves as the backbone of production planning, creating a bridge between customer demand and the manufacturing process. The MPS plan outlines the specific quantities and schedules of products that need to be manufactured, serving as a direct link between sales and production.
In practice, the quantity of items ordered by customers often differs significantly from the quantity that needs to be produced. This discrepancy arises from different production strategies, such as:
- Make-to-Order (MTO): Products are manufactured only after receiving a customer order.
- Make-to-Stock (MTS): Products are produced based on forecasted demand and stored in inventory until sold.
- Assemble-to-Order (ATO): Components are pre-manufactured, and final assembly occurs upon receiving an order.
- Hybrid Strategies: Manufacturers often blend these approaches, producing based on forecasts while maintaining flexibility for custom orders.
The MPS is a schedule that focuses specifically on items and quantities to be produced, regardless of how sales orders are structured. It’s crucial to note that the MPS is not just a reflection of sales orders but also factors in forecasts, safety stock levels, and the company’s production strategy.
A key concept within MPS is stock allocation, which acts as a bridge between sales demand and manufacturing demand. Stock allocation helps determine how much of the sales demand should be met from existing inventory versus how much should trigger new manufacturing orders. This ensures that manufacturing aligns with broader demand while also preventing overproduction or stockouts.
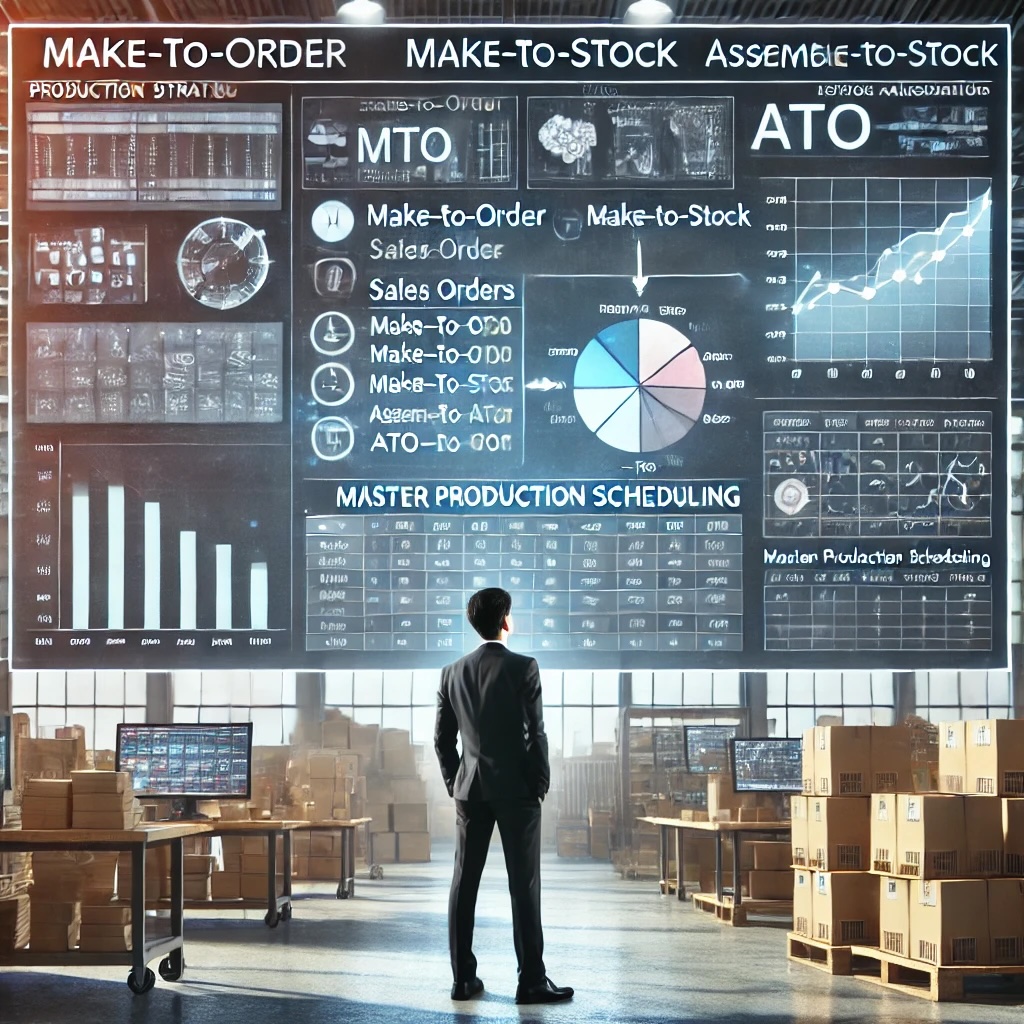
Material Requirements Planning (MRP)
Once the MPS is defined, Material Requirements Planning (MRP) kicks in to manage the detailed planning of raw materials, components, and resources needed to fulfill the MPS. MRP calculates the specific quantities of materials required and ensures that they are available at the right time to avoid delays in production.
MRP’s key functions include:
- Creating detailed production schedules for each component or operation based on the MPS.
- Ensuring that raw materials and subassemblies are delivered to production lines just-in-time to avoid inventory excess.
- Coordinating procurement activities with production schedules to optimize efficiency and reduce waste.
The MRP system dynamically updates as production progresses and new manufacturing orders are received, ensuring that the material flow aligns with the constantly evolving production schedule.
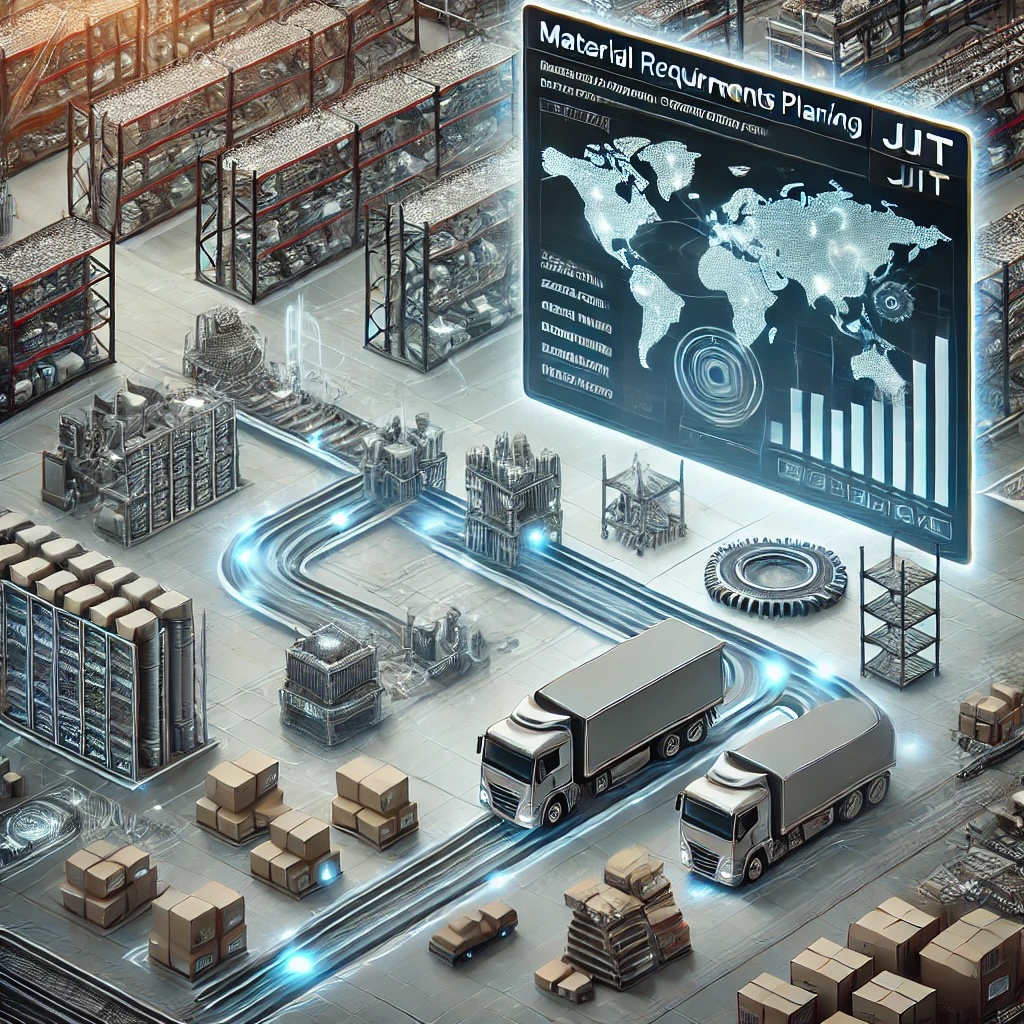
Rough Cut Capacity Planning (RCCP)
While MPS and MRP handle what to produce and the materials required, Rough Cut Capacity Planning (RCCP) focuses on whether the production resources—labor, equipment, and facilities—are available to meet the production schedule. RCCP ensures that the production plan remains feasible by evaluating capacity constraints early in the planning process.
RCCP provides a higher-level view of capacity over a longer time horizon (such as weeks or months) and helps to:
- Evaluate whether sufficient capacity is available to meet the production targets in the MPS.
- Identify bottlenecks in production resources early enough to adjust schedules or allocate additional resources.
- Balance seasonal fluctuations in demand by adjusting resource allocation or production timing.
By analyzing capacity at an early stage, RCCP allows manufacturers to address constraints and avoid production delays or underutilization of resources.
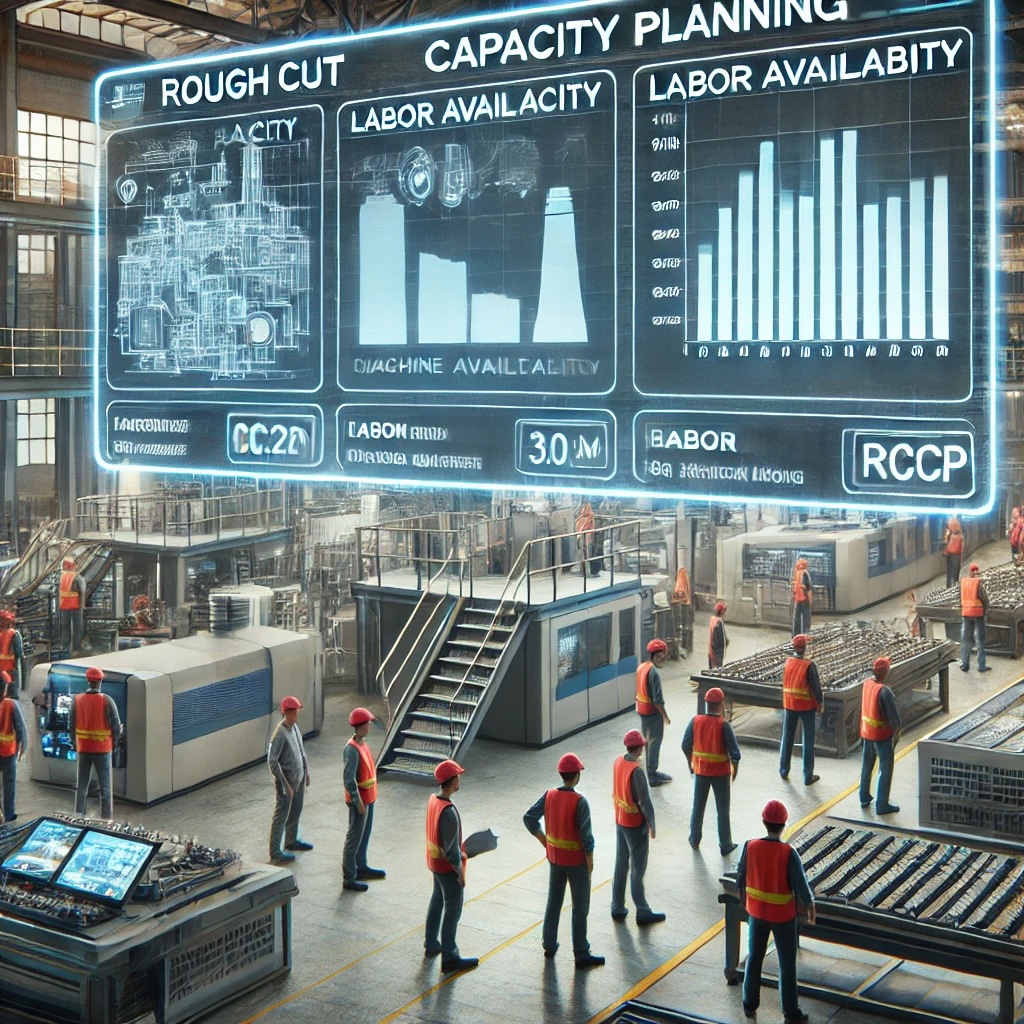
The Synergy of MPS, MRP and RCCP
When integrated into a comprehensive supply chain planning system, MPS, MRP, and RCCP work together to create a seamless planning process that ensures customer demands are met efficiently, without overburdening production resources or running into material shortages. The combined power of these processes allows manufacturers to:
- Align production with customer demand: MPS bridges the gap between sales forecasts and production schedules, ensuring that manufacturing is aligned with both forecasted and real customer demand.
- Ensure material availability: MRP ensures that raw materials and components are available precisely when needed, reducing inventory costs and preventing delays.
- Optimize resource use: RCCP ensures that labor, machinery, and other production resources are used efficiently and that production remains feasible even when demand fluctuates.
By leveraging a well-integrated MPS, MRP, and RCCP framework, companies can increase production efficiency, improve lead times, and better meet customer expectations, all while maintaining lean operations. This approach is essential in today’s fast-paced manufacturing environment, where agility and responsiveness are key to staying competitive.
In conclusion, adopting robust software that incorporates MPS, MRP, and RCCP processes will enable manufacturers to strike the right balance between meeting demand, managing resources, and optimizing inventory levels. This integration is the foundation of modern production planning and essential for operational success.